With magnets and Eddy Current separators we can easily recover metals. But where the magnetic separation reaches its limit, the sensor separation goes a lot further. A certain property such as colour, shape and density can be detected and a blast of compressed air then shoots the detected particle out of the material stream. Also infrared, X-ray and black plastic detection.
Use the Lybover RECYCLING test center and discover concrete and direct results adapted to your situation.
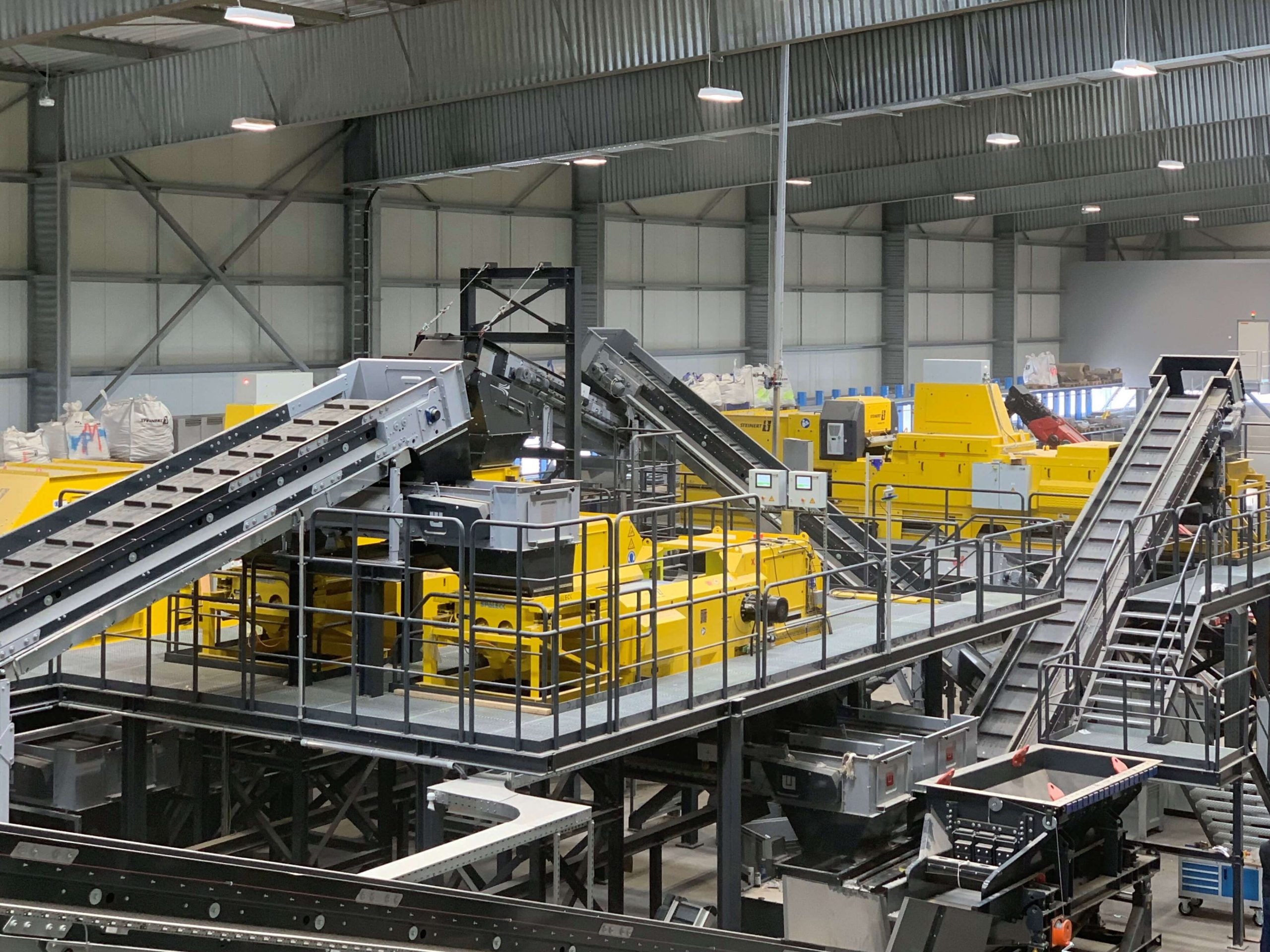
NIR sorting systems
NIR (near infrared technology) refers to a spectrum in a range between 760 and 2500 nm that is invisible to humans. Typical patterns for materials based on molecular vibrations can be detected in this wavelength range after excitation with light.
Even the smallest differences in the chemical composition of the detected materials can be assessed, since the HSI technology deployed by STEINERT is able to observe these typical patterns at very fine resolutions. This has a very effective impact on many applications.
- High spectral resolution
- High optical resolution
- Self-developed technology
Laser-induced breakdown spectroscopy
If light alloy elements are detected in the aluminium, appropriate sorting can be provided with our LIBS technology. LIBS stands for „Laser Induced Breakdown Spectroscopy“. With STEINERT LSS, aluminium alloys can be separated on the basis of magnesium or silicon content, as examples. This then makes further separations within the alloy groups possible.
Unisort Black sorting system
The UniSortBlack technology can be used to separate black plastics and other materials with high potential for reuse from seemingly valueless waste. Waste disposal and recycling companies have the opportunity to develop greater potential for increasing their yields with the UniSortBlack, which sorts these valuable materials out of the waste stream preventing them going to landfill or thermal recovery.
The UniSortBlack makes it possible to save on disposal costs and reduce costs for associated processing. This system can be integrated into existing facilities so that companies can also enhance their sorting concepts using this latest innovation from STEINERT.
Colour sorting system
UniSort Flake – excellent fine product sorting by type or colour
The UniSort Flake is a near infrared sorting unit for separating bulk materials in the fraction range of 3 to 25 mm. It consists of a feed and dispensing device with a material hopper, an acceleration conveyor belt, a containment hood and a compressed air nozzle bar.

The sorting unit is available as “UniSort Flake P” with a high resolution NIR (near infrared) camera or as “UniSort Flake C” with a highly selective colour detection unit.
Sorting can be performed depending on application, e.g. in the case of PET flakes by type or colour. Incorrect colours and unwanted plastics are precisely removed from the PET flow. This ensures very high purity of the sorted material.
Induction sorting system
Produce residual material containing no metal and recover residual metals with the STEINERT ISS® – and at the smallest grain sizes in metal recovery: STEINERT Fines ISS®.
The STEINERT ISS® induction sorting system is the perfect addition to magnetic sorting and eddy-current separation for recovering residual metals from a mix of materials. It is especially suitable for stainless steels and composite materials such as cables or circuit boards. It can be deployed with a focus on producing recoverable metal concentrates, such as zurik or a stainless steel fraction. The aim of treatment may however also be to produce a metal-free residual fraction containing less than 1% metal in order to meet acceptance qualities, e.g. in the production of recovered fuels. Both tasks are the core applications of the STEINERT ISS®.
X-ray sorting systems
High-tech for better processes: x-ray transmission and x-ray fluorescence for a wide range of possibilities to extend the sorting depth.
STEINERT x-ray sorting systems significantly extend the usable information in the raw materials sector for classification of materials by their characteristics and so provide an important contribution to improved recovery of valuable residues and the use of resources.
Our STEINERT XSS® T separates a wide variety of materials for you based on differences in density. Applications range from the sorting of non-ferrous metal scrap into light and heavy metals, ore sorting and the cleaning of secondary fuels through to pre-concentration in the mining industry. The STEINERT XSS T is thus an established sorting system, which also ensures high availabilities even under adverse ambient conditions.
The STEINERT XTS x-ray sorting system is a specific version of our STEINERT XSS® T which satisfies the special requirements in the sorting of diamonds. This system is particularly suitable for the fine grain range.
X-ray fluorescence technology provides a further opportunity to attain more precise knowledge of materials. X-ray fluorescence analysis (XRF) has long been an integral part of chemical analysis in the laboratory sector. The STEINERT KSS sorting system uses x-ray fluorescence to detect and sort, so therefore based on the elemental composition of the sortable material. This means for instance that copper can be distinguished from brass or zinc due to the inherent elements. This is also possible even if the surfaces are heavily soiled, as is often the case with metals from waste incineration. All STEINERT x-ray systems are classified as full-protection devices and thus meet all safety standards to ensure safe operation and handling.
Combination sensor sorting system
The modular structure of the STEINERT KSS sorting machine as a dynamic solution for complex tasks in material separation.
To suit your individual requirements: the STEINERT KSS combination sensor sorting system is a platform on which various sensors can be deployed This includes 3D, colour and induction detection. The system can also be fitted with a fourth sensor (near-infrared, x-ray transmission or x-ray fluorescence sensor).
There is therefore a wide variety of options available depending on the sensor combination:
The combination of 3D detection and induction sensors compared to a purely inductive sensor, for example, enables the active sorting of non-metals from metal concentrates. So-called negative sorting suppresses specific (unwanted) objects in the material flow.
The combination of x-ray transmission (XRT) and 3D provides the option of an additional assessment of object characteristics and makes the system less sensitive to large differences in the material to be sorted.
In principle we always recommend the sensor combination that is configured to customer and application requirements. This combination often opens up further possibilities to clean up generated products beyond the extent originally required or to add sorting stages previously assessed as not feasible.